Pilihan pemasangan dan pembuatan balok busa di rumah
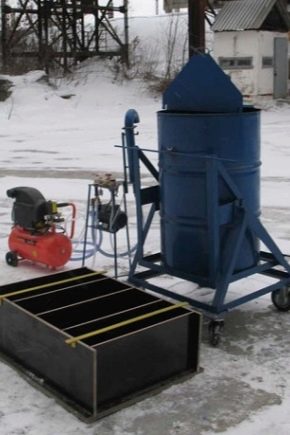
Beton busa adalah bahan yang sangat populer untuk konstruksi bertingkat rendah. Selain produksi industri, juga dibuat secara mandiri. Menerbitkan berbagai jenis blok bisa menjadi bisnis yang menguntungkan. Namun, produksi balok busa di rumah memiliki sejumlah fitur. Sebelum Anda membeli unit yang tepat, Anda harus memiliki gagasan tentang fitur bahan itu sendiri, pilihan alat terkait yang tepat, serta konsumsi campuran yang digunakan.
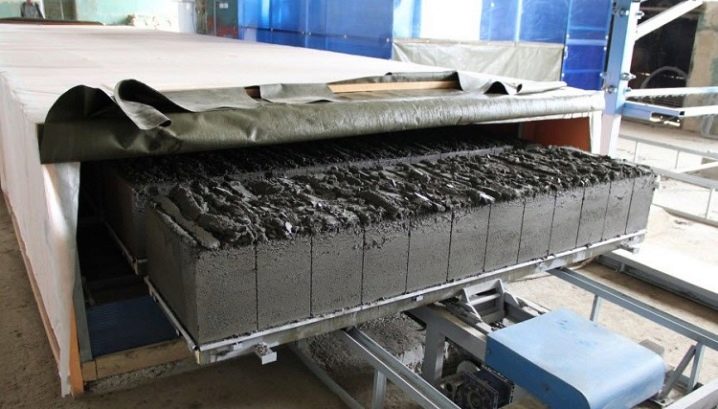
Fitur Bahan
Blok busa terbuat dari mortar, yang meliputi:
- pasir;
- semen portland;
- agen berbusa (konsentrat busa);
- air.
Dalam hal ini, kerapatan curah beton busa bisa berbeda. Bahkan, itu beton dengan struktur seluler. Ini terbentuk karena massa gelembung udara tertutup. Fitur ini menyebabkan kepadatan rendah, serta konduktivitas termal material. Dengan indikator kepadatan yang berbeda, blok busa dapat digunakan sebagai bahan isolasi panas, isolasi panas struktural, dan bahan struktural dengan konduktivitas termal rendah.
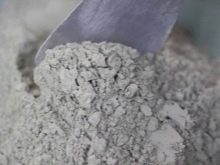
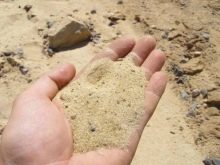
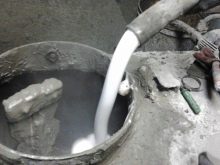
Sebagai aturan, dengan merek beton busa tingkat kepadatannya ditentukan. Semakin rendah, semakin sedikit jumlah campuran yang digunakan untuk membuat bahan. Fakta ini tercermin dalam biaya (beton busa lebih murah daripada beton). Namun, dengan kepadatan yang relatif rendah, itu dianggap sebagai bahan yang menguntungkan untuk konstruksi partisi di dalam rumah.
Blok busa mudah diproses, mentolerir pemotongan dengan gergaji besi biasa. Selain itu, tidak runtuh ketika paku didorong ke dalamnya. Dalam pekerjaan, itu menyerupai kayu, bentuknya persegi panjang. Blok dapat memiliki ukuran yang berbeda: dari elemen standar hingga ekstra besar.
Beton busa buatan sendiri memiliki dimensi yang ditentukan oleh bentuk unit yang dibeli.
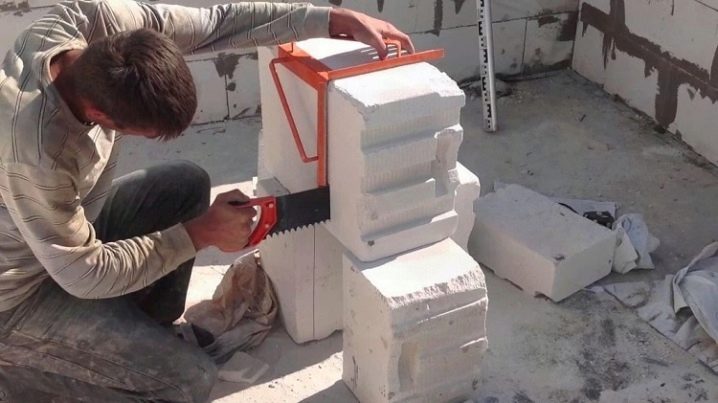
Pro dan kontra
Beton busa memiliki banyak keunggulan karena diminati di industri konstruksi. Bahan ini praktis tidak mengubah kualitas dan karakteristik kinerjanya dari waktu ke waktu, tidak mengalami penuaan. Keramahan lingkungan membuatnya tidak berbahaya bagi kesehatan produsen, pembangun dan rumah tangga. Itu tidak memancarkan zat beracun ke udara, dianggap tahan lama dan andal, dan menjamin isolasi termal yang baik.
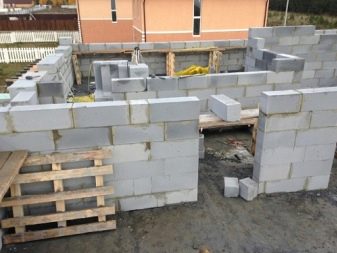
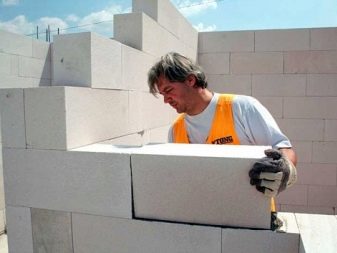
Selain itu, ia memiliki sifat kedap suara yang tinggi, memungkinkan Anda untuk mengurangi tingkat kebisingan, yang penting bagi orang modern. Blok busa lembam terhadap api. Ia mampu menstabilkan latar belakang suhu di dalam tempat, mudah dipasang, dan juga memiliki profitabilitas produksi yang tinggi. Karena bobotnya yang rendah, tidak menimbulkan beban besar, seperti beton. Ini memungkinkan Anda untuk mengurangi biaya pemasangan fondasi.
Namun, selain kelebihannya, beton busa juga memiliki kekurangan. Misalnya, meskipun dianggap tahan lama, ia kalah dari beton dan beton bertulang. Nuansa lain termasuk fakta bahwa blok busa tidak menekuk. Ini juga tidak stabil terhadap kelembaban, karena mampu menyerapnya dari lingkungan.
Terlepas dari apakah bahan itu diproduksi di tempat kerja atau di rumah, itu akan menyusut.
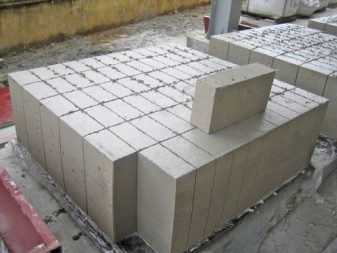
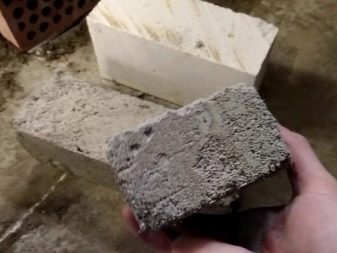
Peralatan dan alat
Dalam pembuatan balok busa di rumah Anda mungkin memerlukan peralatan dan perlengkapan berikut:
- pengumpan untuk semen dan pasir;
- generator busa dengan kapasitas setidaknya 200 l / mnt;
- pengaturan batang;
- dispenser air bekas;
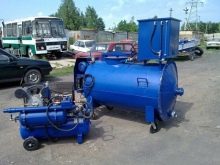
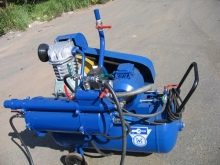
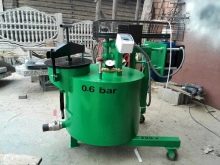
- layar getar (bahan baku ayakan);
- selang untuk keluarnya campuran jadi;
- kompresor;
- mixer beton dengan volume minimal 250 l;
- bentuk khusus untuk balok atau mesin pemotong.
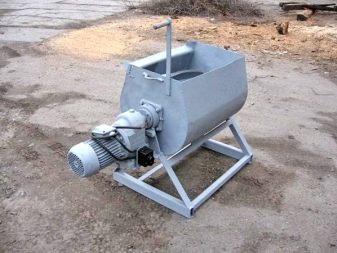
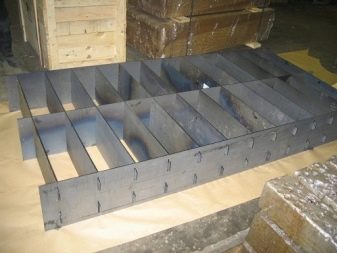
Beli hari ini peralatan yang diperlukan untuk produksi bahan bangunan di rumah tidaklah sulit. Jika diinginkan, Anda tidak hanya dapat membeli lini produksi lengkap, tetapi juga komponen individualnya. Perlu dipertimbangkan bahwa peralatan untuk produksi balok busa di rumah tidak hanya stasioner, tetapi juga portabel. Jalur dapat berupa konveyor atau otomatis. Faktor-faktor ini menentukan biaya peralatan yang dibeli.
Inti dari setiap set peralatan adalah generator busa. Perangkat seperti itu per hari dapat memberikan pelepasan sekitar 100-110 meter kubik material. Ciri khas dari saluran stasioner adalah produktivitasnya yang tinggi bersama dengan kualitas yang sangat baik dan biaya rendah. Mengingat bahwa kit semacam itu akan menelan biaya sekitar 1,5 juta rubel, pembeliannya dipertanyakan.
Pabrik beton busa bergerak tidak memerlukan pembelian generator busa yang mahal, yang membuatnya diminati di pasar konstruksi. Namun, seiring dengan ini, ia juga tidak dapat membanggakan kinerja tinggi. Sebagai aturan, unit tekanan digunakan dalam kasus ini, tetapi untuk semua kekuatannya, ia tidak mampu menghasilkan lebih dari 40-45 meter kubik bahan jadi per hari.
Pada saat yang sama, blok jadi sering dibuat dengan konsumsi konsentrat busa yang tinggi.
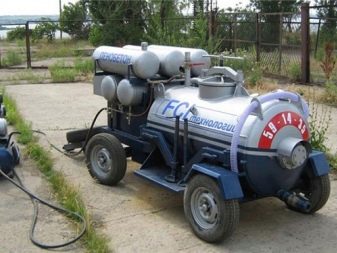
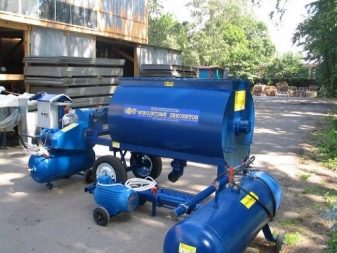
Kekuatan mereka lebih rendah daripada analog yang dibuat pada jalur stasioner. Harga satu set lengkap untuk produksi rumahan dapat bervariasi dari 50 hingga 300 ribu rubel. Dalam hal ini, sebagai suatu peraturan, peralatan berdaya tinggi memiliki biaya tinggi. Misalnya, kit untuk 300.000 rubel dapat menghasilkan sekitar 72 meter kubik beton busa per hari.
Jalur otomatis membutuhkan area yang luas, yang seringkali bermasalah, karena pada awalnya tidak disediakan. Sebagai aturan, jalur seperti itu perlu membuat hopper untuk semen, air, pasir, serta aditif dengan dosis otomatis. Selain itu, perlu dipikirkan area untuk mengeringkan beton busa, menuangkannya ke dalam cetakan, serta memotong instalasi. Peralatan ini mampu menghasilkan rata-rata sekitar 80-100 meter kubik bahan per hari, tetapi tidak semua orang mampu membeli barang mewah seperti itu, karena kit akan menelan biaya 1,5 hingga 3 juta rubel.
Ketika tidak ada cukup uang pada tahap awal, mereka membeli peralatan bekas. Namun, dalam hal ini, Anda harus siap dengan kenyataan bahwa cukup cepat Anda mungkin perlu mengganti suku cadang apa pun.
Selain itu, Anda perlu memahami bahwa peralatan yang sedang beroperasi dapat menyebabkan kualitas beton busa jadi yang buruk.
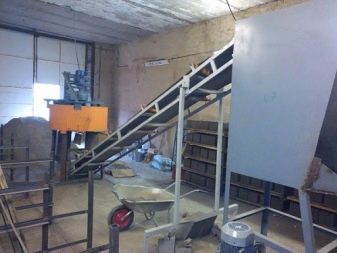
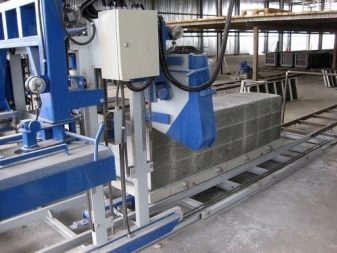
Bentuk yang dibeli untuk beton busa mungkin berbeda. Hari ini mereka terbuat dari baja, kayu lapis, dan plastik. Kapasitas produk berbeda, misalnya, Anda dapat membeli cetakan plastik dengan dimensi 390x190x288 mm, opsi kayu lapis dengan dimensi 588x300x188 mm, rekanan baja dengan parameter 600x300x200 mm. Saat membelinya, penting untuk mempertimbangkan tingkat keparahan geometri, karena kualitas bahan jadi akan langsung bergantung pada ini. Bahkan pelanggaran simetri sekecil apa pun tidak dapat diterima.
Saat memilih cetakan untuk menuangkan massa beton busa, Anda harus memperhatikan bahan pembuatannya. Mengingat bahwa bekisting dapat digabungkan, ini sangat penting. Misalnya, jika penjual mencatat bahwa versi logam dengan sisipan plastik tugas berat mampu menahan suhu tertinggi sekalipun, Anda tidak boleh mempercayai ini secara membabi buta.
Faktanya adalah bahwa bentuk-bentuk seperti itu sebenarnya berumur pendek. Dalam proses pengeringan dan pengerasan massa beton busa, sejumlah besar panas akan dilepaskan.
Plastik, tidak peduli seberapa tinggi kualitasnya, bereaksi terhadap peningkatan suhu.
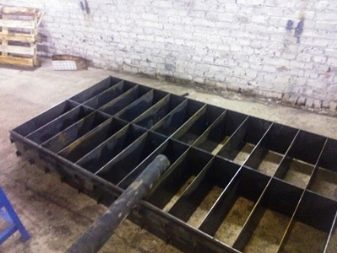
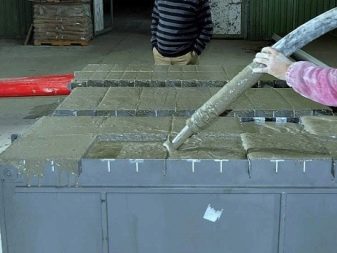
Konsumsi dan proporsi campuran
Proporsi bahan penyusun dalam pembuatan beton busa adalah sebagai berikut: untuk 320 kg semen (misalnya grade M500), 420 kg pasir, 45 liter air untuk mendapatkan busa dan 120 liter air untuk mortar diambil . Adapun konsentrat busa, konsumsinya tergantung pada merek tertentu. Biasanya untuk volume seperti itu digunakan dalam kisaran 1,2-1,5 kg. Air untuk produksi dapat diambil tidak hanya air keran, teknis, kekerasan sedang juga cocok.
Resep dan proporsi secara langsung tergantung pada kepadatan beton busa, yang harus diperoleh pada akhirnya. Misalnya, jika Anda membutuhkan massa jenis blok busa D 600, ambil 210 kg pasir, 310 kg semen, 110 liter air untuk mortar dan 54 liter untuk mengencerkan busa. Selain itu, komponen bahan bangunannya adalah konsentrat busa 1,3 kg dan busa 715 liter. Saat mencampur seluruh jumlah komponen, massa mentah 685 kg akan diperoleh.
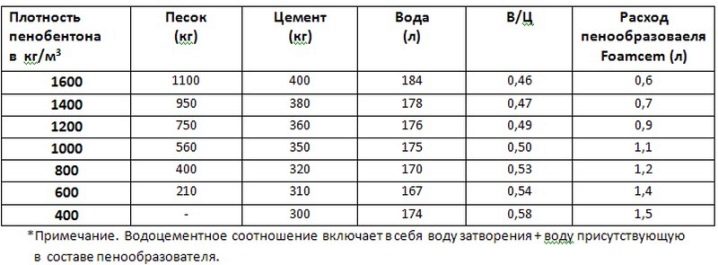
Ketika kepadatan tinggi diperlukan (misalnya, 1000 kg per m3), massa beton busa dibuat dari 590 kg pasir, 350 kg semen, 120 l air dalam larutan, 42 l dalam busa. Untuk resep seperti itu, tidak lebih dari 1 kg konsentrat busa dan 560 liter busa digunakan. Akibatnya, dalam kasus terakhir, massa bahan baku untuk produksi balok busa akan menjadi 1103 kg.
Penting untuk memantau keseragaman busa dan larutan yang dihasilkan. Ini akan meningkatkan karakteristik kualitas bahan jadi. Saat memilih resep yang tepat, harus diingat bahwa menurut GOST saat ini, penyusutan bahan jadi tidak boleh melebihi 3 mm per 1 sq. m.
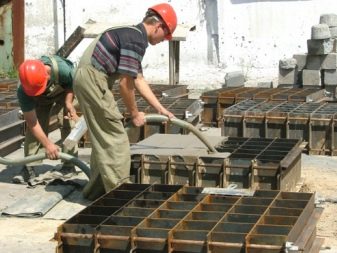
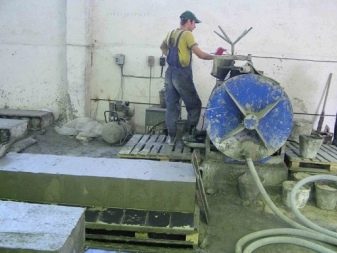
Bagaimana melakukan?
Produksi balok busa di rumah dilakukan dengan dua cara: pengecoran dan penggergajian. Teknologi manufaktur do-it-yourself klasik melibatkan penggunaan formulir tipe kaset khusus dengan partisi dan sisi yang dapat dilepas untuk membagi wadah total menjadi bagian terpisah dengan ukuran yang sama. Dalam bentuk seperti itu, solusinya mengering dan mengeras, setelah itu beton busa jadi dihilangkan. Keuntungan utama dari metode pembuatan bahan bangunan ini adalah kenyataan bahwa blok monolitik tidak perlu dipotong.
Ini menghilangkan kebutuhan untuk membeli mesin gergaji, yang mengurangi biaya peralatan. Namun, itu adalah bentuk yang dapat menyebabkan pelanggaran geometri yang ketat.Tidak semua elemen yang dituangkan ke dalam cetakan setelah pengerasan akan sempurna bahkan ketika membeli perlengkapan yang mahal. Pernikahan akan dalam hal apa pun, dan ini adalah biaya tambahan dari campuran yang digunakan.
Untuk mencegah penghancuran blok busa, perlu menggunakan pelumas khusus yang terurai di udara terbuka selama beberapa hari.
Zat semacam itu tidak murah, tetapi jika tidak digunakan, ini dapat menyebabkan keripik atau retakan pada blok busa.
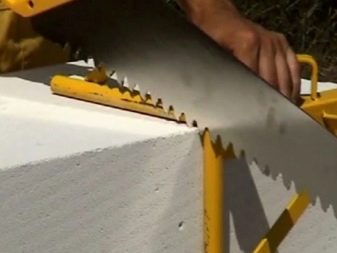
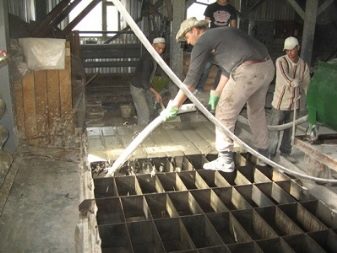
Paling sering dalam produksi rumah, teknologi pemotongan digunakan. Dalam hal ini, satu cetakan besar pertama kali dituangkan, yang kemudian dipotong menjadi elemen individu dengan ukuran tertentu. Untuk metode ini, mesin gergaji dibeli. Meskipun akan membutuhkan investasi keuangan tertentu, profitabilitas akan meningkat. Keuntungan dari metode ini adalah geometri yang ketat dari setiap elemen, serta meminimalkan pembentukan chip di tepi blok busa.
Namun, teknik ini dapat menghabiskan uang dengan baik, karena diperlukan peralatan khusus untuk menghasilkan blanko kecil, dan harganya mahal. Selain itu, memotong pelat monolitik menjadi potongan-potongan kecil meningkatkan waktu yang dihabiskan untuk produksi material.
Ada dua jenis mesin pemotong. Dalam kasus pertama, ini adalah unit di mana bahan monolitik dipotong segera setelah mengeras (deformasi). Ini nyaman karena Anda tidak perlu memindahkan seluruh pelat ke mesin gergaji, sehingga mengurangi biaya dan waktu tenaga kerja. Pemotongan blok busa terjadi karena senar khusus, ditandai dengan akurasi pemotongan yang tinggi.
Kerugian dari elemen pemotongan ini adalah kerapuhannya, serta biaya yang layak.
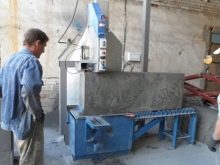
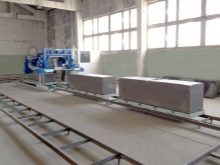
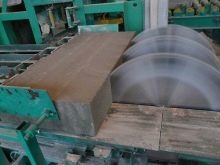
Jenis instalasi pemotongan kedua perlu mentransfer monolit beton busa untuk dipotong. Dalam hal ini, harus dipotong dengan bilah tipe disk. Tidak seperti senar, pisau semacam itu tahan lama, dan unit itu sendiri ekonomis untuk dirawat. Namun, mentransfer pelat beton busa ke mereka, secara halus, tidak nyaman dan merepotkan.
Pengerasan blok busa dapat dilakukan dengan dua cara: alami dan autoklaf. Pada saat yang sama, elemen yang dikeringkan dengan metode kedua memiliki karakteristik kualitas terbaik. Jadi adalah mungkin untuk menciptakan kondisi yang paling menguntungkan untuk mendapatkan bahan bangunan yang baik. Namun, harga peralatan tersebut secara signifikan menyentuh kantong, jadi ketika diproduksi dalam jumlah kecil, itu tidak dibeli.
Beton busa yang mengering sendiri lebih baik mengering di musim panas. Sebagai aturan, jika suhu di dalam ruangan selama pengeringan minus, Anda harus menutupi bekisting atau memikirkan pembuatan ruang khusus untuk mengukus blok busa. Dalam kasus pertama, polietilen atau batting industri biasanya digunakan. Yang kedua, sebuah ruangan dialokasikan untuk kebutuhan ini di dalam bengkel produksi.
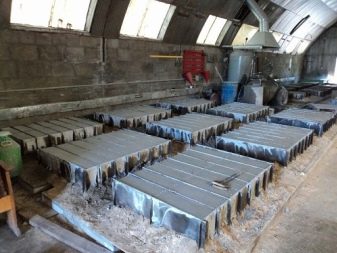
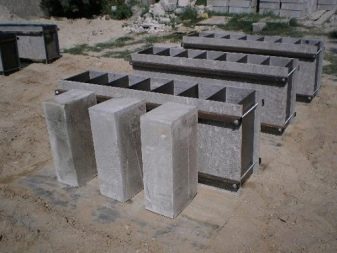
Di ruangan seperti itu, rezim suhu khusus dibuat, dengan mempertimbangkan kelembaban yang diperlukan untuk pengerasan balok yang seragam dan tepat. Seringkali, generator uap digunakan untuk tujuan ini, sehingga mencoba untuk mengotomatisasi alur kerja. Ketika tidak ada uang tambahan, tetapi Anda tidak ingin menambah waktu pengeringan balok busa, mereka menggunakan opsi anggaran yang berbeda untuk menyelesaikan masalah ini. Seseorang meletakkan ember air di dalam ruangan, dalam kasus lain, komunikasi dengan pemanas gas dilakukan ke dalamnya.
Mereka yang tidak puas dengan solusi ini melampirkan bagian tertentu dari ruang produksi dengan beberapa bahan yang tersedia yang dibedakan dengan harga yang dapat diterima. Misalnya, batu bata tua, lembaran berprofil atau bahkan balok busa yang sama digunakan sebagai pagar. Saat mengukus ruang dengan gas, perlu memperhitungkan optimalitas mode yang dipilih. Idealnya, kelembaban dalam ruangan tidak boleh kurang dari 65%. Namun, jika produksi tidak menyediakan pembelian peralatan khusus dalam bentuk ruang panas dan kelembaban, ini dapat mempengaruhi sertifikasi bahan jadi.
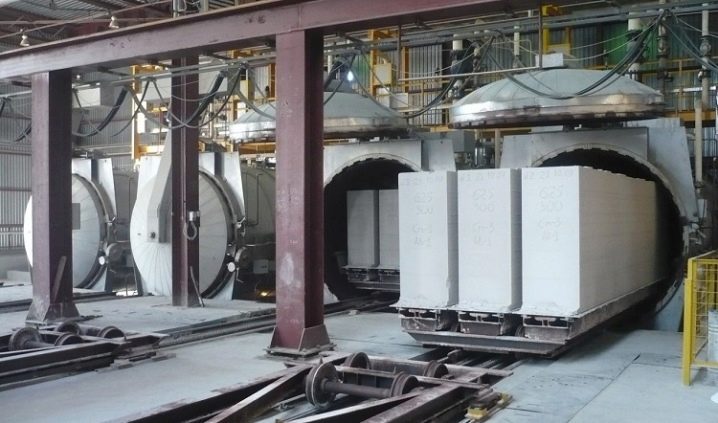
Teknologi manufaktur
Teknologi standar untuk pembuatan balok beton busa di rumah terdiri dari beberapa operasi.
- Awalnya, konsentrat busa disiapkan dalam wadah terpisah. Kemudian dikombinasikan dengan air dan dikirim ke pembangkit uap. Jika produksi sendiri memiliki unit kavitasi yang membuat busa isinya menggunakan ultrasound, langkah ini akan dilewati.
- Pada tahap selanjutnya, perlu menyiapkan campuran untuk beton busa. Untuk melakukan ini, komponen campuran yang diperlukan dan aditif khusus ditempatkan di ruang mixer. Setelah itu, ruang diisi dengan busa yang disiapkan sebelumnya. Menurut aturan teknologi, pencampuran di dalam ruangan terjadi dalam beberapa menit.
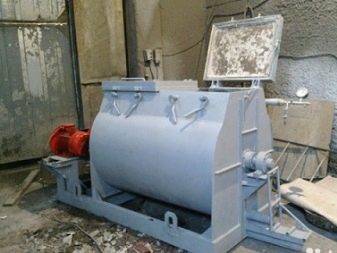
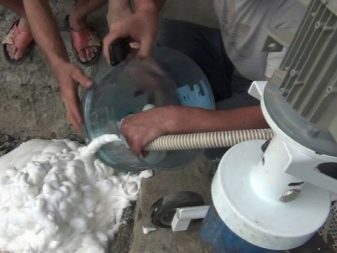
- Jika unit kavitasi digunakan dalam produksi, awalnya, agen berbusa ditempatkan di ruang untuk pencampuran. Dalam hal ini, komponen yang tersisa dari solusi kerja ditempatkan kemudian. Dalam hal ini, waktu pengadukan tidak boleh lebih dari 0,5 menit. Pada tahap ini, larutan siap untuk dituangkan.
- Setelah diaduk, komposisi dituangkan ke dalam bentuk yang ada. Untuk mencegah massa menempel ke permukaan peralatan, titik kontak dilumasi sebelumnya dengan oli mesin atau cairan pelumas khusus. Diinginkan bahwa suhu di dalam ruangan selama pemadatan dan pengerasan komposisi setidaknya +20 derajat ° C. Setelah sekitar 8-10 jam, beton busa akan mendapatkan seperempat kekuatannya.
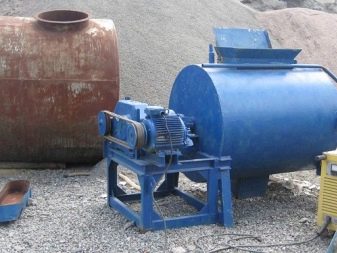
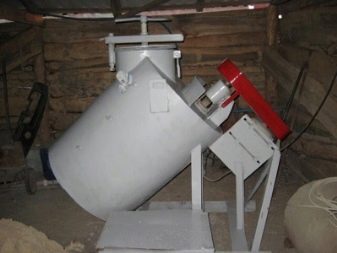
Ini adalah waktu terbaik untuk memotongnya, dengan mempertimbangkan dimensi yang diperlukan, serta pengemasan. Kekuatan akhir elemen diperoleh setelah 28 hari sejak tanggal pembuatannya. Kekuatan pelepasan dianggap sepertiga dari yang ditentukan.
Anda dapat menjual barang dalam dua hari.
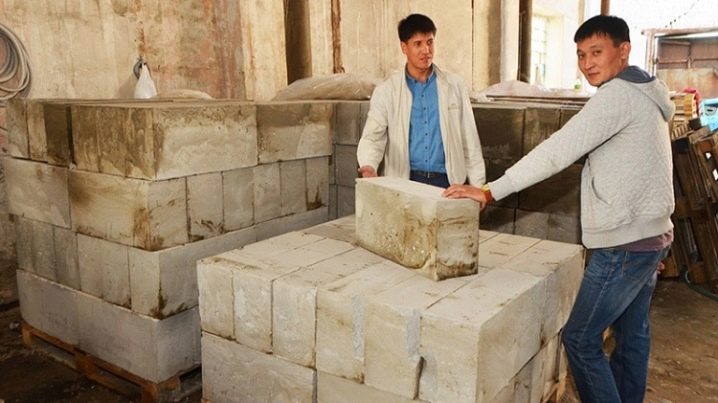
Apa yang harus dipertimbangkan?
Kadang-kadang tampaknya jauh lebih mudah untuk membuat peralatan untuk produksi balok busa sendiri, menggunakan pengetahuan dasar, perhitungan daya, dan gambar yang tidak sulit ditemukan di Internet saat ini. Namun, pada kenyataannya perlu dipertimbangkan: pembuatan beton busa di pabrik mini rumah tidak memungkinkan ketidakakuratan, karena manfaatnya tergantung padanya. Anda perlu memahami bahwa dalam kasus ekstrim, produk pabrik tidak akan sulit untuk dijual di masa depan karena tidak perlu, sementara produk buatan sendiri akan tetap tidak diklaim.
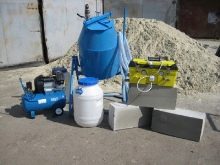
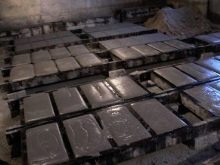
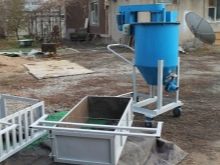
Untuk produksi blok busa, semen Portland grade M 500 digunakan. Untuk meningkatkan karakteristik kualitas elemen jadi, berbagai aditif ditambahkan ke dalamnya. Misalnya, menggunakan pengubah Bio NM, Anda dapat meningkatkan ketahanan balok busa terhadap embun beku. Karena aditif "Bio-Lux" dan Laston, dimungkinkan untuk meningkatkan konsentrasi udara dalam struktur material.
Agar bahan jadi memiliki sifat insulasi termal yang sangat baik, bahan pembusa tipe industri harus dibeli untuk pembuatannya.Tidak peduli seberapa banyak Anda ingin menghemat uang dan membuatnya sendiri, itu tidak akan memiliki indikator retensi panas yang mirip dengan opsi yang dibuat dalam produksi.
Penting juga bahwa bahan baku berkualitas tinggi adalah dasar dari blok busa berkualitas tinggi.
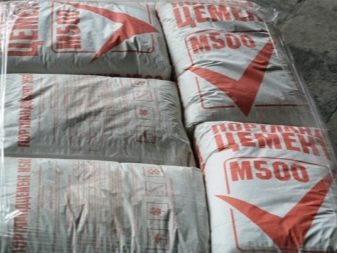
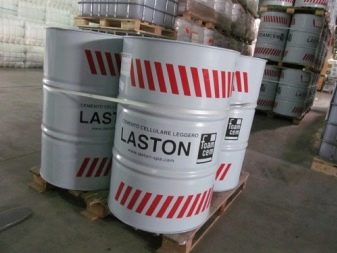
Anda dapat menemukan instruksi untuk membuat blok busa di rumah dengan menonton video di bawah ini.
Komentar berhasil dikirim.